
Sheets made this way will be labeled "bamboo lyocell" and they'll probably be more expensive than viscose options. After pulling back the covers on the bamboo sheet industry and analyzing the options currently available, researchers concluded that lyocell is "considered to be one of the leading methods of producing environmentally friendly regenerated fibers for textiles" in a 2016 paper in the journal Fashion and Textiles 2. This method uses slightly gentler solvents, repurposes them in a closed-loop system, and tends to be more eco-friendly. Sheets made using a viscose process will typically be labeled "viscose made from bamboo" or "rayon made from bamboo." (In the U.S., they legally can't 1 just be called "bamboo" because of all this processing.)īamboo sheets can also be made using a lyocell production method.

This method comes with a few environmental concerns, which you can read up on here. Most bamboo sheets are made using a viscose process: The bamboo is broken down, crushed, mixed in a bath of chemicals, and then spun into yarn. This requires the use of chemical solvents, so although bamboo on its own is a natural fiber, bamboo sheets are heavily processed. First, its pulp needs to be broken down and turned into a fiber that's soft enough to sleep on.
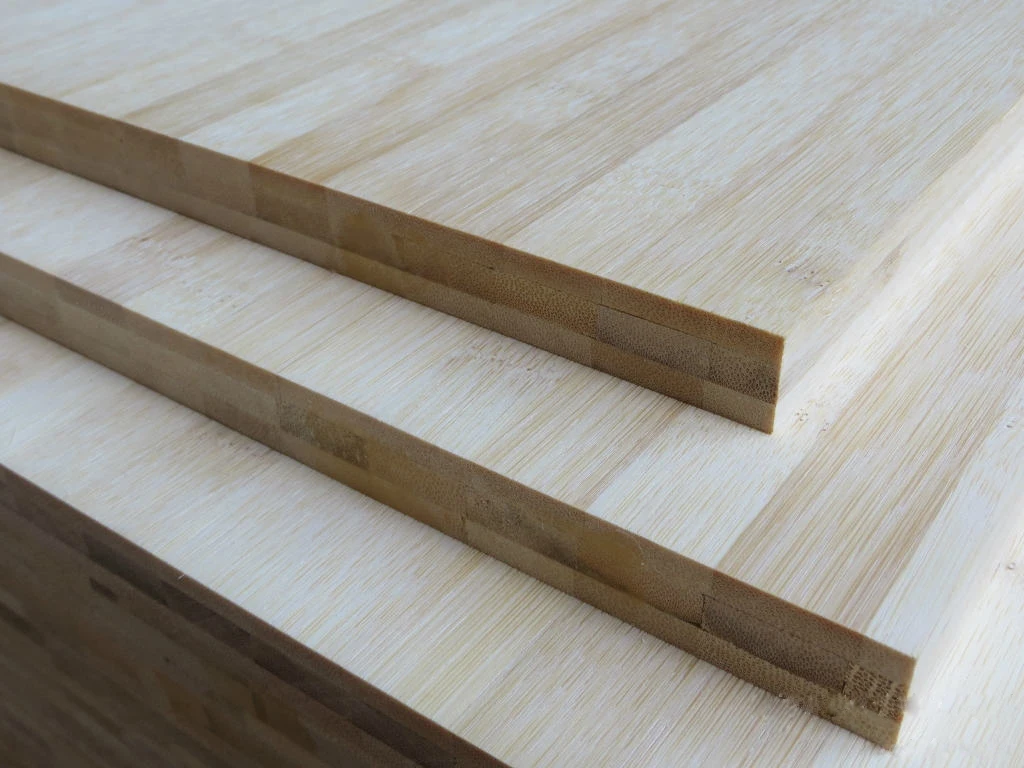

"You can do that for decades without replanting it, whereas when you cut a tree down, that's it."īut obviously, the bamboo that's harvested isn't quite ready to drape your bed just yet. "Because it's so prolific and renewable, you can pull about 50 million pounds of bamboo fiber annually from about 1,000 acres once it reaches maturity," David Knight, the founder of multiple companies that incorporate bamboo, previously told mindbodygreen.
